Injection Molding:Revolutionizing Plastic Manufacturing
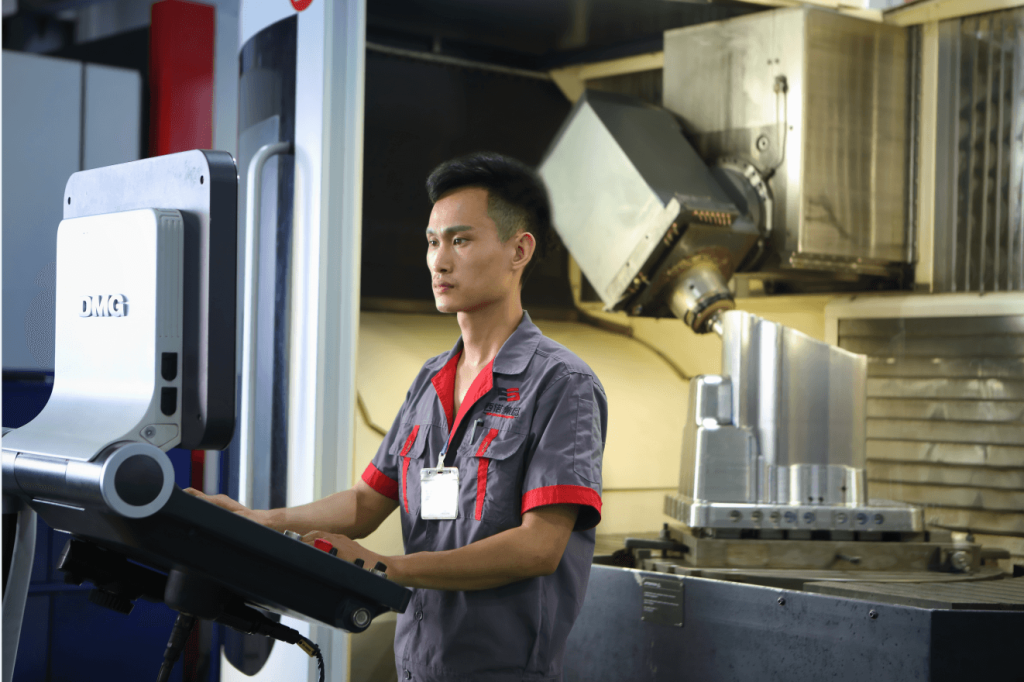
Introduction
In this article, we’ll explore the fascinating world of injection molding, a revolutionary technique that has transformed the plastic manufacturing industry. From its inception to the latest advancements, we’ll delve into the process, benefits, applications, and future trends of injection molding. So, let’s dive in and discover how this remarkable method has shaped the world around us.
What is Injection Molding?
Injection molding is a manufacturing technique that encompasses the injection of melted material, usually plastic, into a cavity within a mold. Once the material solidifies, it is ejected from the mold, resulting in the creation of a precise and durable product. This highly versatile technique allows for the mass production of complex shapes with excellent dimensional accuracy.
The Process of Injection Molding
The injection molding process consists of several key steps:
Clamping: The mold halves are securely closed, ensuring the mold cavity is airtight.
Injection: The molten material is injected into the mold cavity under high pressure.
Cooling: The material cools and solidifies within the mold, taking the shape of the cavity.
Ejection: The mold opens, and the product is ejected, ready for further processing or use.
Benefits of Injection Molding
Injection molding offers numerous advantages, making it a preferred choice in various industries:
Cost-effective: Injection molding enables high-volume production, resulting in lower unit costs.
Design flexibility: Complex geometries, intricate details, and undercuts can be easily achieved.
Rapid production: The fast cycle times allow for quick turnaround and increased productivity.
Consistency and repeatability: Injection molding ensures consistent part quality with minimal variation.
Wide material selection: A vast range of thermoplastics can be used, offering diverse properties.
Enhanced strength and durability: The final products exhibit excellent structural integrity.
Applications of Injection Molding
Injection molding finds applications across numerous industries, including:
Automotive: Production of interior components, exterior body parts, and precision-engineered parts.
Consumer Goods: Manufacturing of consumer electronics, appliances, and household items.
Medical: Creation of medical devices, laboratory equipment, and disposable components.
Packaging: Production of bottles, containers, caps, and other packaging materials.
Aerospace: Manufacturing of lightweight components, including aircraft interior parts.
Electronics: Production of connectors, switches, housings, and other electronic components.
Types of Injection Molding Machines
Injection molding machines come in various types, each suited for specific requirements:
Hydraulic Machines: Versatile and widely used, offering high pressure and excellent control.
Electric Machines: Energy-efficient and precise, ideal for cleanroom environments.
Hybrid Machines: Combining hydraulic power with electric precision for optimized performance.
Two-Shot Machines: Capable of injecting two different materials or colors in a single cycle.
Vertical Machines: Suitable for over molding, insert molding, and other specialized applications.
Choosing the Right Injection Molding Machine
When selecting an injection molding machine, several factors should be considered: